IoT — Internet of Things — is a buzzword nowadays. If you read tech-articles and they are not about Artificial Intelligence, they will be about IoT for sure. Since the term “Industry 4.0” already feels like something outdated and “Digitalization” is quiet unspecific, the term Industrial Internet of Things (IIoT) is en vogue to discuss IoT especially in production [1]. There are plenty of statistics from analysts and consultants showing you the potential of IIoT (e.g. [2]). But after evaluating the first IIoT use cases you quickly notice: many use cases fail the business evaluation due to the initially required investment. And the single use case you realize just adds another layer of complexity to your operational technology. So, let’s have a look why — besides all existing statistics — IIoT must be relevant for production in the future and why IoT platforms play a crucial role in this game.
IoT vs. IIoT
In general, we talk about IoT when we connect physical “things” to the internet so that they can communicate with each other and use the computing power of servers [3]. When we talk about things, we mean daily used objects we never thought of connecting to the world wide web before. They exchange information with other things in a way that we maybe even do not notice that they communicate via internet at all. [4] For example Smart TVs or Smart Watches: Do you notice when they are online? Or have you ever thought of connecting your TV and watch to the internet 15 years ago? Besides connecting them to the digital world, the world wide web, they can also be connected to the physical world. Via sensors such as cameras, temperature sensors etc. they gather information from their environment. They use this information to store and proceed it to servers worldwide and exchange them with other devices. Meteorological stations are good examples. They collect data about wind and rain via sensors all over the world and store them in one common place to allow accurate weather forecasts.
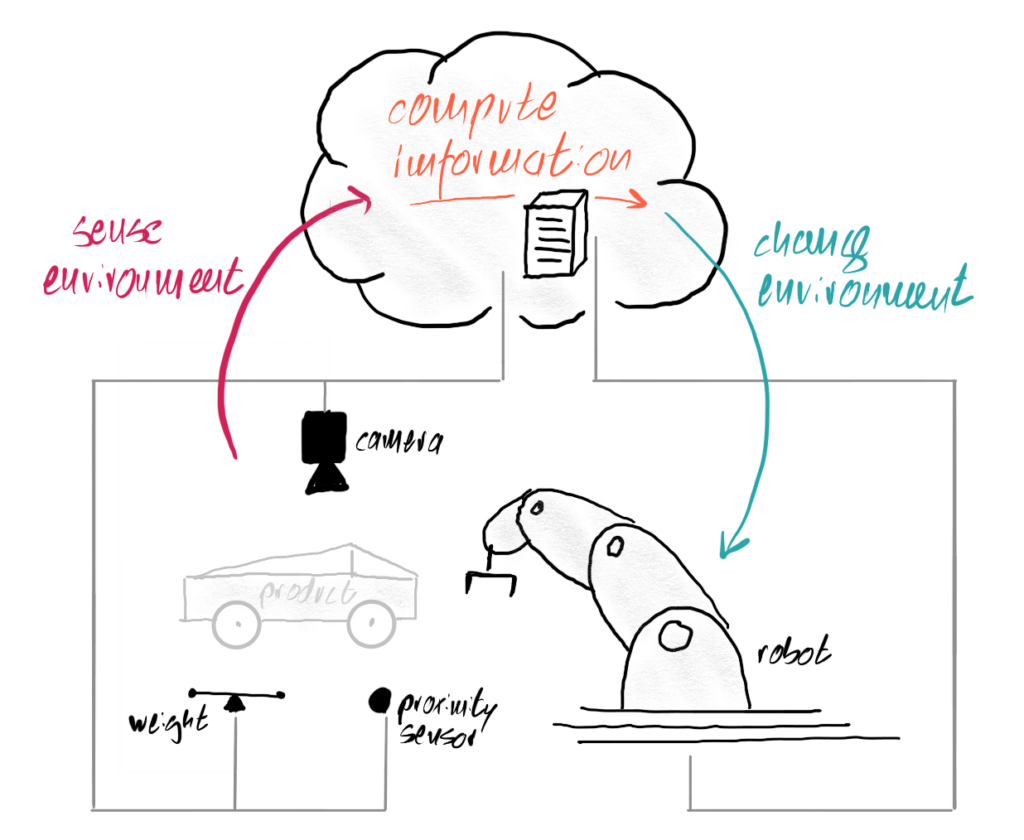
When we apply the idea of IoT to production, we talk about IIoT. Or Industry 4.0. Or digitalization in production. Or maybe even Cyber Physical Systems. But in general, the approach is the same: existing and additional sensors give you insights into how your production is performing, control the flow of goods and give you the possibility to analyze and improve. This can be cameras for visual quality control, scanners to trace products, vibration and temperature sensors to monitor a machine or tools with integrated RFID-readers to check whether you use the right torque to fix the screw. The potential of IIoT is immense and there are much more than only these few use cases. E.g. McKinsey analyzed an economic impact of 1.2 to 3.7 trillion Dollar for production by 2025 [2].
Although the idea of IIoT is the same as IoT, the challenges in production are slightly different:
- You are often faced with rather old machines with the same old controls and you have no possibility to connect and gather data directly from existing sensors. The same problem occurs if you own the machines, but your service agreements with the supplier do not allow you to do any changes to it. And sometimes you are not faced with these constraints, but you simply do not have the knowledge in your team to access and edit the control’s code.
- If your Smart TV’s latest update breaks your Netflix-app, it is annoying, but not critical. But if your machine breaks down, this becomes critical. Very critical. Of course, your IIoT solution must not cause this risk. Usually, that is the reason why you only want to read data from existing sensors and never want to write any data to a machines’ control. The alternative is to do a retrofit. This means, you install additional sensors and connect them to your network without touching any components of the machine.
- The first Industry 4.0 use case you want to implement is easy. As long as the setup does not change, it can be transferred to different machines, production lines and plants easily. The second use case you want to implement is similar. But then comes the tricky part: the more use cases you realize, the more different hardware, software, suppliers and integrators are involved. And of course, each of them has different preferences and requirements. Due to the fact that you always have to consider the existing environment, the complexity grows exponentially with every additional use case.
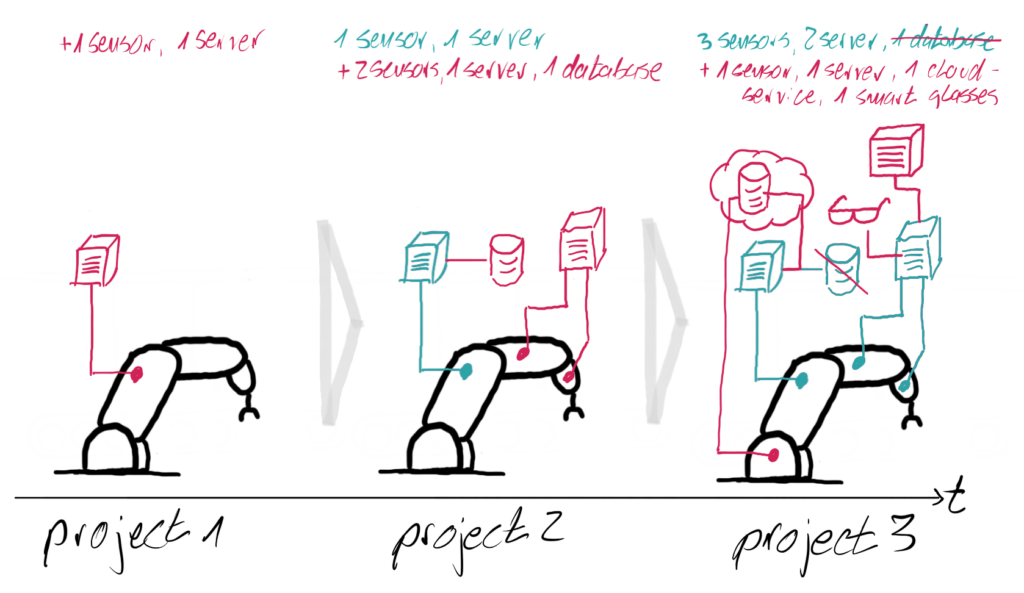
Need of IoT platforms in production
This is when IoT platforms come into play. Of course, (almost) no hardware manufacturer changes his or her hardware just to adopt to your unique requirement. As well as only a few software providers will exclusively implement another proprietary protocol and interface for you. Like Lego-bricks with different sizes and shapes, the hardware and software components you want to integrate do not fit together. They need common interfaces or adapters to work with each other. And that is more than “they all use Ethernet-cables”. It also refers to the communication protocols and exchanged data packages. The internet is a good example of harmonization among heterogenous parties. Nowadays, APIs with JSON as exchange formats are commonly used. For IoT, lightweight protocols such as MQTT are also widespread. Nevertheless, you need an entity in your network which is able to convert a bouquet of different protocols and data packages into one common standard you defined to ensure connectivity and flexibility. Besides, all these IT-driven use cases add more and more software solutions to your environment. Software, which is not like an ERP “one monolith doing it all”, but lean, specialized solutions for only one certain scenario. Besides translating between all the different languages everybody is using, you also need to manage all these small applications in one place. Many IoT platforms work like the app-store on your mobile: you do not download applications from unreliable sources anymore and install them yourself like you did with Windows 95. You simply go to the app-store and e.g. download the calculator-app you only want to use for calculations.
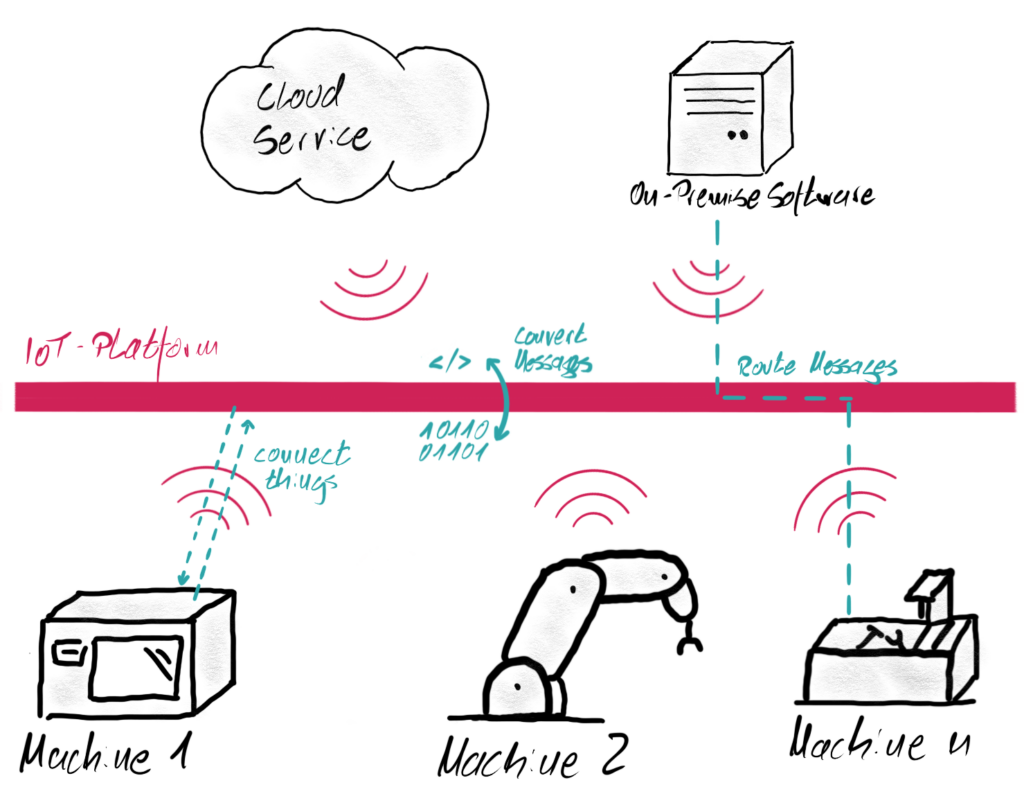
Converting different protocols and managing all applications in one place is what most IoT platforms do. They ensure compatibility between existing applications and provide a common interface for future extensions. Other than that, they control the flow of information between the entities. Thereby, IoT platforms help you to save engineering and maintenance efforts for implementing new adapters, migrating existing software, ensuring security, cleaning up outdated applications and debugging problems. These advantages become more and more crucial for today’s complex production infrastructures. Years ago, you implemented an IT-solution every 10 years. In the age of Industry 4.0, you change your infrastructure much more frequently.
But if everything seems so promising, why do companies hesitate to implement IoT platforms? The problem is, that you first need to set up the IoT platform, migrate existing protocols and interfaces to one defined standard, and connect all your production assets with it. This means much effort and higher costs at the beginning of your digitalization journey before you can really benefit from the advantages of the IIoT-world. And of course, if you calculate your return on investment (ROI) based on one use case, this huge effort does not pay off. Besides, you can not name all potential future use cases yet, which makes it even harder to calculate a ROI for several use cases instead. A lot of good use cases just pop up as soon as your users and employees start working with IIoT. From a management point of view, a decision based on numbers and short-term benefits will most likely never be positive for an IoT platform.
Given this fact, what other arguments are there to convince yourself (and your management) to start your IIoT journey? In engineering, the concept of “frontloading” is well-known. Frontloading means, you accept higher efforts at the beginning of a project or product development process, in order to save even more effort later. In requirements engineering, this is done by a design phase in which you first conceptualize what you want to do before you start developing. In agile product management, this is done by early MVPs and prototypes to evaluate feasibility and business potential before you start the development of a full product. And for technical implementations, this is done by first implementing a scalable, maintainable infrastructure and backend which gives you a chance to leverage synergies later when you start to work on features and use cases. An IoT platform is this kind of infrastructure which will save you integration and maintenance efforts in the future. Instead of tinkering on another fragile solution, you re-use your given APIs. Instead of spending hours to understand the flow of information and the consumption of services and tools in your production before you can start to fix a problem, you manage them all in one platform. And instead of laborious migrations of many coupled services because one is outdated, you just exchange the affected part.
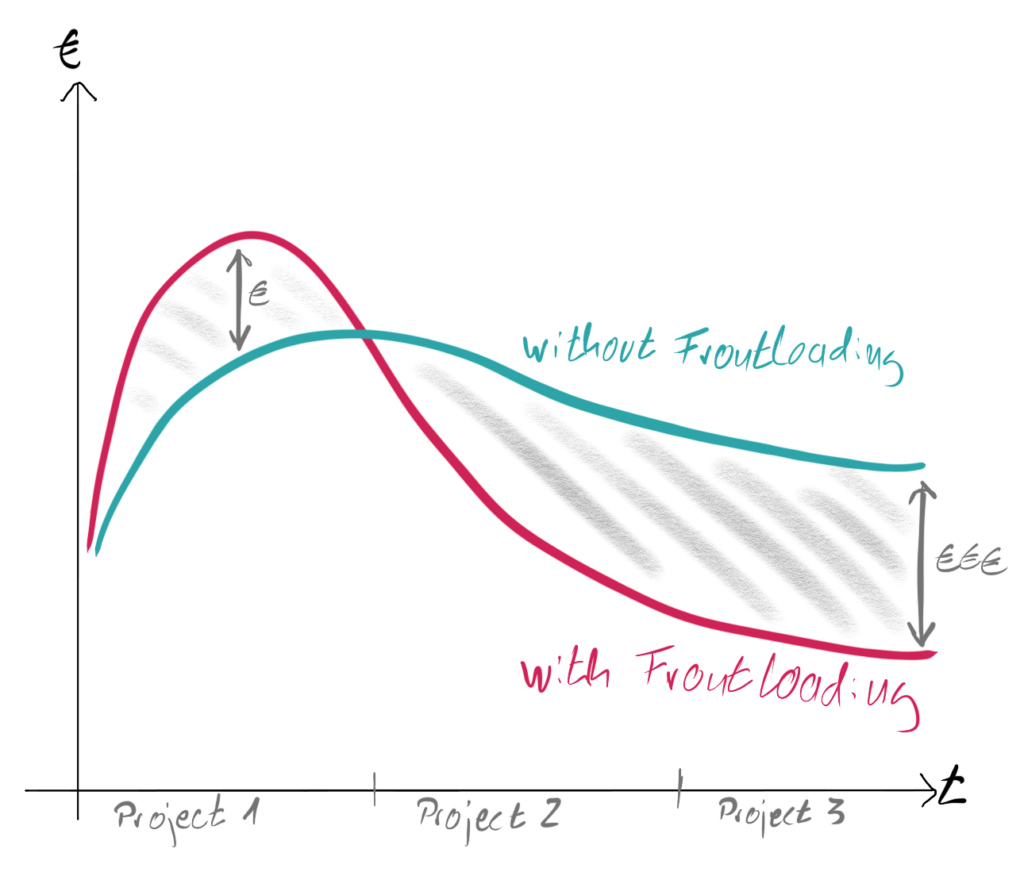
TL;DR (aka “summary”)
To sum it up, IoT platforms give you higher flexibility, transparency and maintainability of your infrastructure. Besides, they enable your production to become a smart factory by adopting future Industry 4.0-driven use cases in an ease of time. Nevertheless, it is almost impossible to calculate a satisfying ROI for one single use case. Frontloading is the reason why the investment into IoT platforms pays off. But still, you can hardly put the advantage into numbers and it only makes sense if you plan to realize several use cases. Given this fact, the decision for “real” Industry 4.0/ IIoT depends on your belief whether digitalization is a game changer and your company, especially your colleagues, will come up with new innovations after the first steps. Today’s situation is similar to the Lean-movement of the 1990s: Just introducing Kanban does not improve your company, but implementing the Lean-philosophy with all its facets brings your company forward. If you nowadays have a look what impact “real” Lean had on production and talk to early adopters of IIoT, maybe this will finally convince you.
Sources & further reading
[2] McKinsey — Unlocking the potential of the Internet of Things (2015)
[3] F. Mattern, C. Floerkemeier (2010): From the internet of computers to the internet of things
[4] M. Weiser (1991): The Computer for the 21st Century. Scientific American.
[5] D. Kolberg, M. Göke (2019): Die digitale Datenautobahn — Rückgrat der Digitalisierung